CNC Cameras
modular, coolant-resistant cameras to see inside of operating CNCs
Closer, clearer views from different angles allow operators to better understand exactly where the machine is and what it is doing, reducing crashes and downtime. The modular design, compatible with a wide array of camera modules and lenses, allows the cameras to be mounted anywhere for a variety of purposes, from wide-angle views of the full machine interior to distortion-free close-ups of tooling.
An air blade and positive-pressure sealing system prevent coolant and chip buildup in from of the lens and coolant intrusion to the camera body. An automated system hooked into the machine’s coolant loop ensures that the air system only runs when it is needed. The camera module itself is suspended on a vibration-isolating mount to prevent machine vibrations from interfering with image quality. The front glass (acrylic) can be replaced through the removal of only a single screw, by sliding in and out. This allows the front, which is expected to be a wear item due to chip impacts, to be easily replaced. It also makes access to the camera lens easy in the event focus needs to be adjusted.
For safety reasons the case was designed so that all pressure-bearing elements are metallic: the aluminum body and camera plate, and an aluminum plate backing the retaining ring (not shown above). Metallic components are stronger and fail more predictably than 3d printed parts, reducing the odds of a catastrophic structural failure while the case is pressurized. Furthermore, the case is typically pressurized only when the doors are closed and the machine is operating, and the case runs at an adjustable pressure lower than shop air pressure.
As of writing, cameras have been installed in every metal-cutting CNC at the Bechtel Innovation Design Center at Purdue University: two lathes and four mills. They are accessible to all CNC users through the computers at each control, displaying camera feeds, allowing users to switch between different cameras on each machine, and providing recording and streaming capabilities. The current arrangement provides close-up views of the spindle to monitor tool positioning on each machine and wide views of the full machine interior on the larger machines.



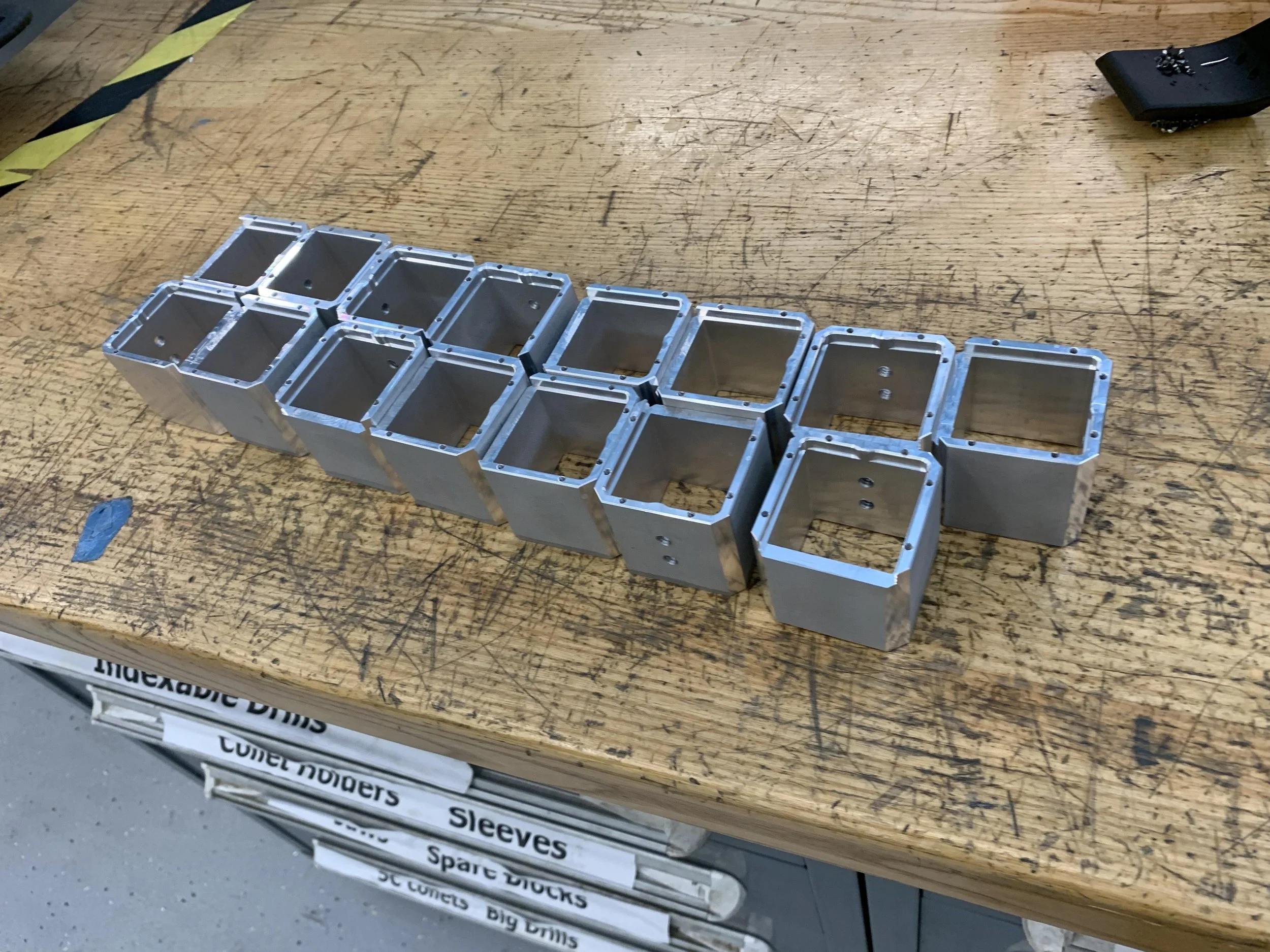


